VACUMM FORMED TRAYS
Vacuum Formed Trays, also named Plastic Trays, Shipping Trays, ESD Trays, and Insert Trays, are commonly used for packaging applications due to their lower cost tooling, ability to run thin material a large number of design features.
Thermoforming is made up of several similar processes. These include vacuum forming, pressure forming, and twin sheet forming. They all have applications with plastic packaging. Vacuum forming is used for more basic trays and is the least expensive option. Pressure forming adds pressure to the part pressing the plastic against the mold. Pressure forming is better for great detail, close tolerances, and small cavities. Twin sheet forming essentially welds two sheets of plastic together, allowing for hollow or reinforced parts. Twin sheet forming is used for skids, trays with fork truck access, or trays requiring two surfaces.
Although simplified somewhat, vacuum forming is similar to thermoforming (which produces comparable results).
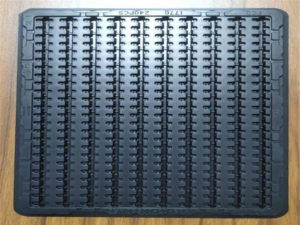
Vacuum-formed trays are used for material handling applications (i.e., moving parts or components around a factory or supply chain). They are manufactured by heating a sheet of plastic which is then stretched over a mold before being forced against it by a vacuum. Once cooled and removed from the mold, a plastic tray is produced.
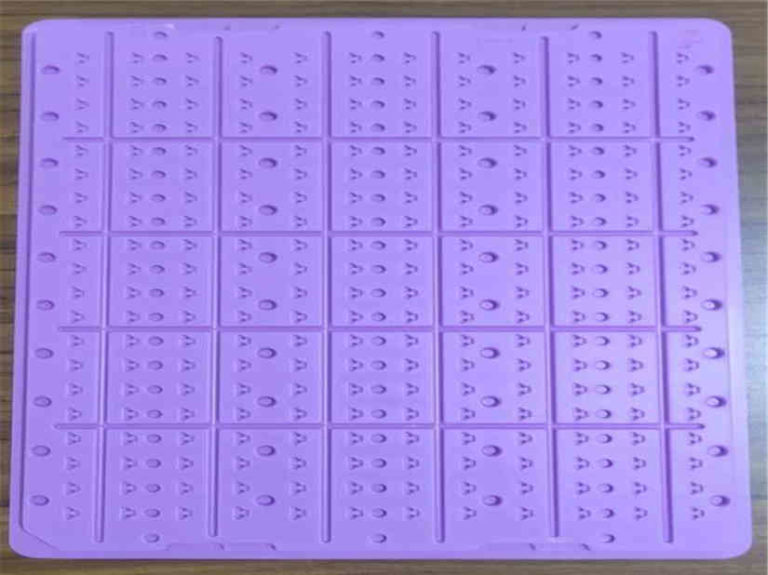
ADVANTAGES OF VACUUM FORMED TRAY PACKAGING
- 1. Low part cost and cost per component. Trays are also low in weight reducing shipping costs.
- 2. can streamline the packaging process saving significant time while properly protecting parts.
- 3. Minimises movement (and therefore damage) during handling
- 4. Can be tailored to your product / component(s) for optimum fit
- 5. Large number of material options including ESD materials and antistatic materials.
- 6. Thin material / nesting for saving space when not in use
- 7. Trays can be made to a specific even number like 50 or 100 cavities per tray facilitating counting.
- 8. Ideal for high volume requirements, and protecting high value items
HOW TO DESIGN VACUUM FORMED TRAYS
While it is possible to source vacuum-formed trays with standard cavities, the real benefits of using vacuum-formed trays/inserts come through the range of customized options available.
Firstly, the cavities can be shaped to be a very close fit to your specific part, product, or component. This, in turn, offers additional protection to your items by minimizing any movement during handling or transit.
Similarly to this, the layout of any cavities within the vacuum-formed packaging can also be altered, allowing you to maximize the efficiency of your handling trays (effectively getting as many parts as possible within the outer container).
Tray Stacking allows for the tray to stack with no load on electronic components and parts. This is usually done with 180 degree rotational stacking or with 90-degree rotation. Undercuts can also be used for stacking if rotation is not an option.
The use of different material colors can also tie in with your company’s branding while also helping to distinguish between similar components, batches, or items.
This can also be achieved through additional molding of instructions or part numbers (something which can also be achieved with labeling).
Finally, it is possible to create anti-static trays using ESD-safe material. These are an excellent solution for the safe handling and storage of electronics.
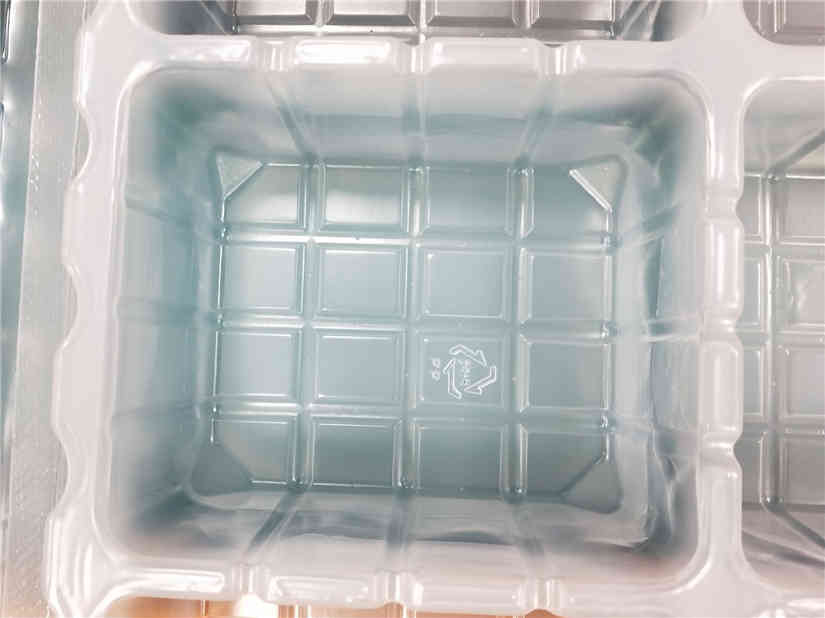
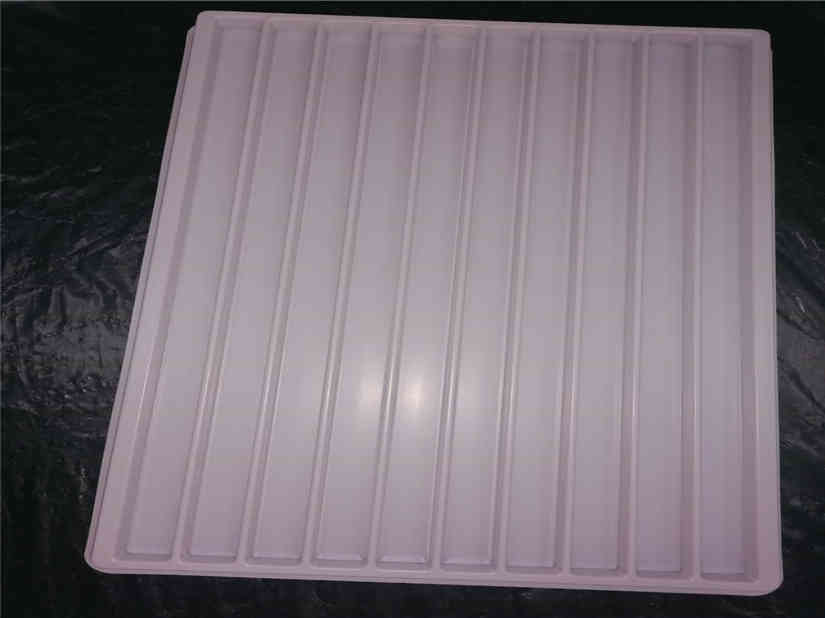
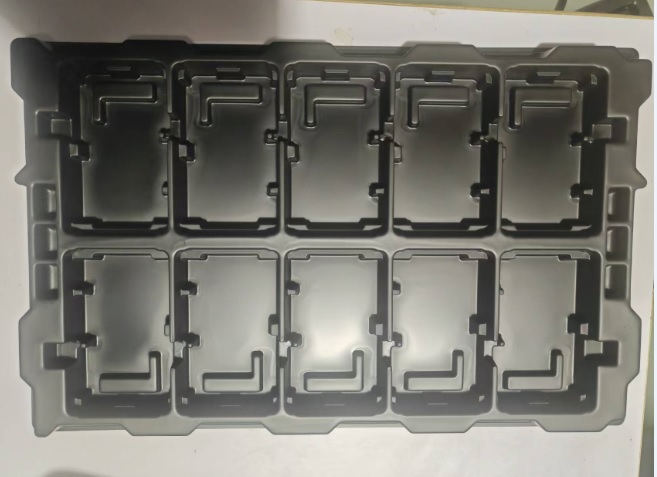
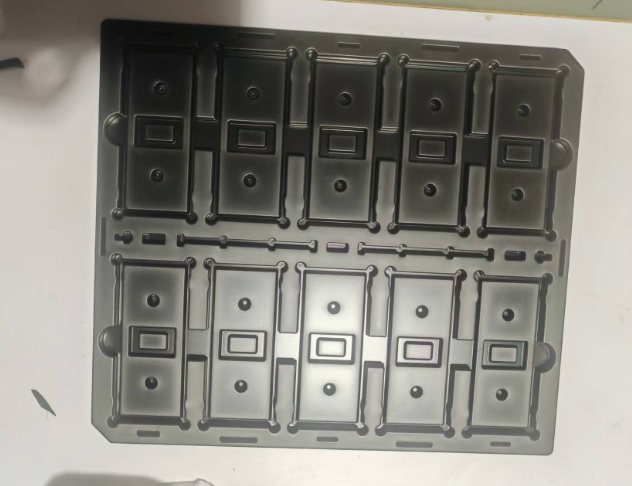
What material to be choosed
Material Selection is a key decision when specifying a tray. Key variables when choosing a material include, ESD requirements, impact resistance, budgetary constraints, operating temperature, chemical resistance, cleanliness with regard to applied coatings, clarity (clear vs. opaque), color, and sealing technique if applicable.
Material Considerations
- Cost
- ESD Requirements
- UV Resistance
- Chemical Resistance
- Coatings applied to materials for ESD protection
- Durability
- Heat Deflection
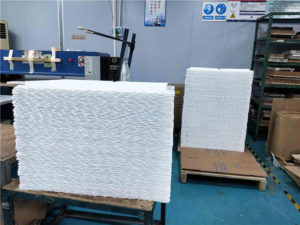
Custom Trays Material Thickness
- Plastic Material Thicknes
1) .015″ to .030″ starting thickness is common for disposable shipping trays for small parts.
2) .030” to .060” starting thickness for use for a number of cycles but not long term.
3) .060″ to .375” starting thickness for long term reusable trays. - Molded Pulp Material Thickness(2 options)
1) .⅛” standard gauge molded pulp. This is typically used for shipping and lighter items.
2) .250” heavy gauge molded pulp is very durable used for skids, trays, and heavier parts.
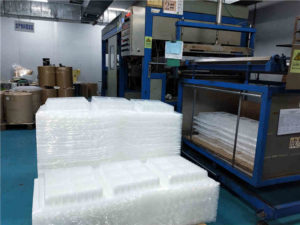
ESD Tray Materials (Shipping & Reusable Trays)
- Anti-Static PVC
- For shipping applications and not for long-term use. The coating will become less effective with time and use. This is generally a thin gauge option in .030 starting thickness—surface Resistivity of material 10e^9.
- Conductive Styrene Black
- The material can be used for semi-reusable and reusable trays as ESD properties are set in the material. It is not a coated material. Surface resistivity 10e^4 to 10e^7. Black Conductive Styrene is generally a thin gauge option with a .030” starting thickness.
- PETG Anti-Static Material
- Description: For shipping applications and not for long-term use. The coating will become less effective with time and use. This is generally a thin gauge option in .030 starting thickness. Surface Resistivity of material 10e^9.
- ESD Material(a heavy gauge for reusable material handling trays)
- HDPE Blue Ant-Static Material(heavy gauge)
- Anti-static, generally blue, do not hold a charge for very long. A charge of 5000 volts is fully decayed in less than 2 seconds. This material requires a relative humidity of 15% or greater, so it won’t do the job in very dry atmospheres. The advantage of this material is that it does not slough conductive particles and is therefore usable in cleanroom situations. Trays meet minimum specifications per MILB-81705B. The base material, high density polyethylene, has high impact strength. It is tested to less than 1012 ohms per square inch.
- HDPE Black Conductive(heavy gauge)
- Conductive containers are always black because the material contains carbon black. The carbon black allows the containers to conduct, and therefore if grounded, they will not create an ESD moment. The conductivity of the containers is a permanent part of the high-density polyethylene material used to manufacture the containers. There is, however, a tendency for minute particles of the carbon black to slough. This trait may make the containers unacceptable in certain clean rooms. Surface tested to ensure that it is 105 or fewer ohms per square inch.
- Conductive ABS(heavy gauge)
- They are used for long term ESD applications—storage trays, etc. Expensive compared to conductive HIPS(above) and compared to standard ABS. See R63 Data Page.
- Inherently Static Dissipative PETG
- They are used for long-term ESD Trays. Storage and Handling trays. Expensive compared to conductive HIPS(above) or compared to standard PETG. This material has a blueish tint.
Common Materials For Shipping | Reusable Trays (Non ESD)
High Impact Polystyrene (HIPS Tray Material used for shipping and reusable trays)
Thin and heavy gauge options. Low cost material for shipping or reusable trays comparable in price to PVC Clear. Styrene is readily available in black and white. Styrene is more rigid than PVC with the possibility of cracking on corners with reuse.
HDPE Tray Material(used for shipping trays in special applications and for automotive trays)
Thin and Heavy Gauge options. Material is softer, has good impact strength, and excellent chemical resistance. It is also good for low temperature applications.Disadvantages include tendency to warp which make it difficult to use for trays that need to be flat for automation applications. Also very difficult to bond to HDPE.
PVC(used primarily for small parts shipping trays)
Advantages: 1. Low cost 2. Durable (longer lasting than styrene in comparable thickness) 3. Clear 4. Good chemical resistance 5. Available in ESD with a anti-static non silicone coating (see ESD Options)
Disadvantages: 1. Generally has a denesting agent allowing trays to be separated when nested. This is an applied coating which often includes silicone 2. Due to silicone coating, may not be good option for medical applications depending on sensitivity of application
PETG Material(used for shipping trays and reusable trays)
Thin and Thick gauge options. PETG is a Clear Polyester. It has excellent strength for use in packaging trays and is a low outgasing material. Common applications include medical and optics. It may have a de-nesting agent similar to PVC which can be silicone. Also available with an Anti-Static Coating, Inherently Anti-Static, or Un-Coated.
Polypropylene(often used in medical trays for shipping or storage)
Polypropylene has unique chemical resistance properties, and resists heat allowing it to go through some sterilization processes like autoclave. Often used in medical applications. PP is a softer material and also can be difficult to maintain flatness.
Polycarbonate(used in high heat applications and for lab trays)
Polycarbonate is more expensive by a factor of 5 compared to the low cost packaging items. Key advantage to using polycarbonate is the higher heat deflection temperature (see below). Recommend testing in specific application.
Heat Deflection Temperature: 270 degrees Fahrenheit
Continuous Use Temperature (= 24/7): 180 degrees Fahrenheit
Intermittent Use Temperature: 257 degrees Fahrenheit
ABS Material(primarily for reusable trays)
Thin and heavy gauge options. Material has good impact resistance. It is often used with drip trays or automation trays as material stays flat. Most common color is black. Fairly low price but more expensive than Styrene, PVC, and PETG.
Foam Material(rigid)
Foam trays are available in Polyethylene and Polyurethane in multiple densities and in Anti Static and Conductive materials. Polyethylene is a stiffer material better if parts have weight. Polyurethane is a softer material potentially better if parts scratch easily.
Keep reading: What are the materials for Anti Static Plastic IC Shipping Tubes
FAQs(Frequently asked questions about vacuum formed trays)
What is the difference between vacuum forming and thermoforming?
Vacuum forming and thermoforming are effectively the same process of heating plastic to a malleable temperature before forming it to a specific shape. The difference however in vac forming is the additional process of using a vacuum to force the plastic material to conform to the mold.
What plastic can be used for vacuum forming?
A number of differing plastics can be used for vacuum forming. This includes vacuum forming grades of ABS, PETG sheets and – most commonly – HIPs (High Impact Polystyrene sheets). Vacuum formed trays are commonly manufactured from HIPs.
Is HIPs recyclable?
Yes, HIPS and other polystyrene products can be recycled and this therefore minimizes the effect on the environment. Besides this, High Impact Polystyrene is cost effective to produce, meaning it’s use is widespread in the food industry.
What is the vacuum forming process?
As mentioned above, vacuum forming is effectively a version of thermoforming. A sheet of plastic is heated to a specific temperature (known as the forming temperature), and is then stretched onto a single-surface mould. The material is then forced against the mold by a vacuum.
Are vacuum forming tools expensive?
The answer depends on what you are comparing the costs to! For producing tote inserts and vacuum formed trays, the tooling cost is significantly high. However, when compared to other tooling, such as that for injection molding, vacuum formed tools are relatively low cost.
Contact us in Linkedin to learn more information